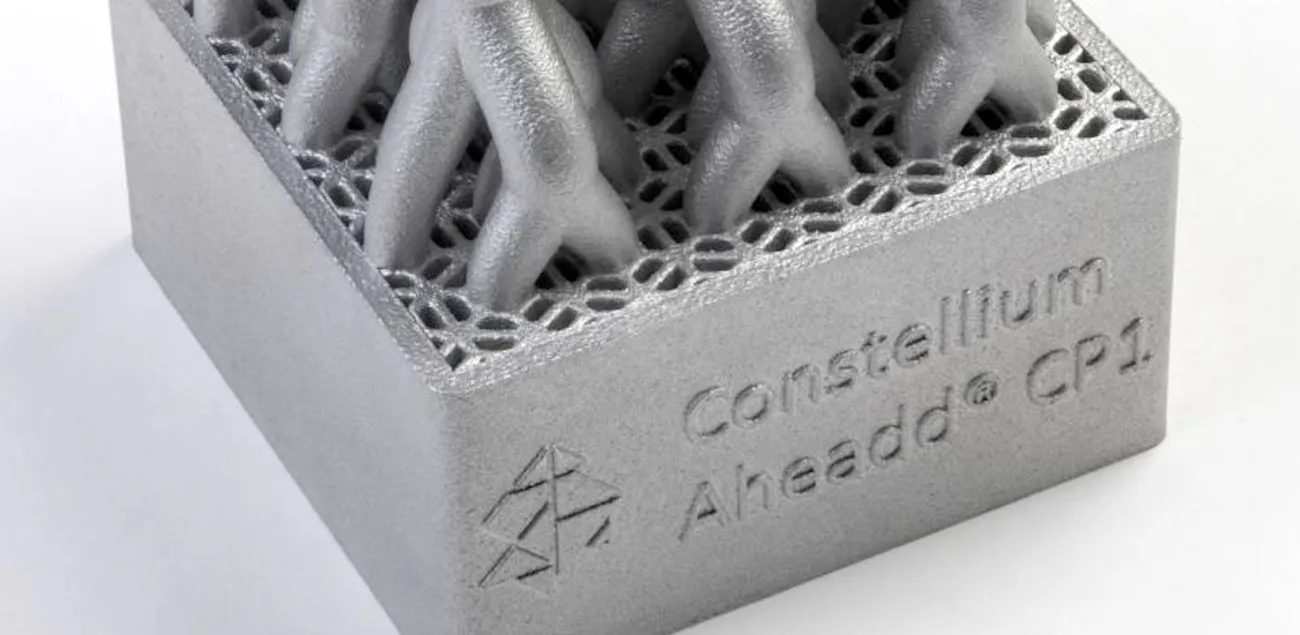
Constellium Joins Large-Scale Pentagon Programme
The French metallurgical group Constellium has entered into an agreement with the American company Nikon Advanced Manufacturing and the public-private partnership America Makes to implement a project focused on the use of a specialized aluminium alloy in additive manufacturing. The initiative is geared towards applications within the US defense and aerospace industries. With a budget of $2.1 million, the project is funded by the US Department of Defense and will be managed by America Makes. Other key collaborators providing guidance include top defense contractors like Lockheed Martin and Northrop Grumman.
As part of this collaboration, Constellium will supply its Aheadd CP1 aluminium alloy, a material containing zirconium and iron additives that was specifically developed by the company's engineers for laser powder bed fusion. This form of 3D printing is designed to create highly complex and detailed metal parts. The Aheadd CP1 alloy has already demonstrated its potential in the manufacturing of critical, high-stress components, such as heat exchangers, and has been approved for producing parts for Formula 1 racing cars.
The project's primary objective is to evaluate the properties of the Aheadd CP1 alloy and subsequently qualify it as a material suitable for the stringent requirements of the defense and aerospace sectors. This effort is a component of a much larger program aimed at maximizing the use of additive technologies in companies that support US national defense. All data obtained from the testing will be shared with US Department of Defense partners through the Workbench for Additive Materials information database. The Pentagon's focus on additive technologies is driven by their ability to accelerate the production and repair of weapons and equipment. Notably, 3D printing can be used to create 'disposable' spare parts for aircraft repair, allowing for faster component replacement compared to traditional manufacturing methods.
New Use Found for Niobium
The Japanese corporations Toshiba and Sojitz, in partnership with the Brazilian company CBMM, have developed a new type of lithium-ion battery that utilizes an anode made of niobium and titanium instead of traditional graphite. While graphite is a common material for anodes in lithium-ion batteries, it has a significant limitation: during rapid charging, a layer of metallic lithium can form on the surface of the graphite anode. This deposition increases the risk of short circuits, which in turn reduces the lifespan and safety of the battery.
The use of titanium and niobium oxides as the anode material effectively prevents the deposition of metallic lithium. This innovation ensures the durability and safety of the batteries, even when they are subjected to frequent high-power charging. According to Toshiba, the predicted service life of such a battery is at least 15,000 charge cycles, a substantial improvement over existing battery models and a key factor in potentially reducing the overall cost of electric vehicles and electronic equipment.
Toshiba has already begun to supply samples of these new lithium-ion batteries to its customers. The batteries have been tested in an electric bus at the industrial site of CBMM in Brazil. CBMM's involvement in the project is central, as the company produces over 100,000 tonnes of niobium per year, making Brazil the world's largest producer. It is followed by Canada with 7,100 tonnes, Congo with 700 tonnes, Russia with 350 tonnes, and Rwanda with 200 tonnes annually.
Niobium is currently used for alloying steels for large-diameter pipes, in the manufacture of high-capacity electrolytic capacitors, for cryotrons in computers, and in uranium and plutonium fuel elements for nuclear reactors. The project by Toshiba, Sojitz, and CBMM could establish an entirely new market for the metal.
Oman to Become a Hub for Lithium-Ion Battery Production
Hunan Zhongke Electric, a Chinese manufacturer of materials for lithium-ion batteries, intends to invest $1.1 billion to construct and launch a plant for producing anode materials in the Sohar Free Economic Zone in Oman. The project is planned to be implemented in two phases, with each phase launching production of anode materials with a capacity of 100,000 tonnes per year, for a total of 200,000 tonnes. The first phase is scheduled for completion three years after the start of construction.
The global market for lithium-ion battery materials is currently experiencing rapid growth, driven by the expansion of electric vehicles and portable electronics, as well as the increasing use of renewable energy sources and storage devices. The market's value is expected to reach $12.3 billion by the end of this year, with projections for it to expand to $26.3 billion by 2030. Anode materials are a critical component of these batteries, directly influencing parameters such as charging speed, service life, energy density, and safety.
Last year, Hunan Zhongke Electric supplied 225,700 tonnes of anode materials to its customers, generating nearly $700 million in revenue. Its client list includes major lithium-ion battery manufacturers such as CATL, BYD, LG Energy Solution, SK On, and Samsung SDI. The Sohar Free Economic Zone, where the new anode plant will be built, has already attracted over $30 billion in foreign capital investment. Under recently signed agreements, a solar power plant and a wind turbine manufacturing plant are also planned for the zone. Together with the Hunan Zhongke Electric plant, these projects will help create a cluster for the production of clean energy equipment and stimulate demand for various materials, while also helping to diversify Oman's economy, which has long been based on the extraction and export of hydrocarbons.
East Hope Group Wants to Produce Aluminum in Kazakhstan
China's East Hope Group plans to implement a large-scale, vertically integrated aluminum complex in Kazakhstan. According to the company's plans, the complex will include a bauxite mining and processing plant with a capacity of 6 million tonnes per year, a primary aluminum smelter with a capacity of up to 3 million tonnes per year, and a wind farm to supply them with energy. East Hope Group intends to carry out the project in three stages, utilizing modern and environmentally friendly technologies. The total investment is estimated at $12 billion, and the project is expected to create 10,000 permanent jobs.
East Hope Group has extensive interests in the global non-ferrous metallurgy industry, as well as in agriculture, construction, chemicals, and power engineering. It is owned by Liu Yunxin, one of China's wealthiest individuals. However, the company's primary focus is non-ferrous metallurgy. In 2019, it signed a memorandum of understanding with the Khalifa Industrial Zone administration in the United Arab Emirates, which provided for investments of up to $10 billion. The first phase of that project included an alumina plant, followed by a waste treatment plant and an R&D center, and finally plants for non-ferrous metals production. However, there has been no information about the successful implementation of this project to date, and it is possible that it was halted.
In Kazakhstan, East Hope Group will face competition from Eurasian Resources Group, which owns the Kazakhstan Electrolysis Plant with an annual capacity of 250,000 tonnes of aluminum. This plant receives 1.5 million tonnes of alumina from Aluminium of Kazakhstan (also part of Eurasian Resources Group) and supplies another 1 million tonnes to Russia. Eurasian Resources Group had previously considered increasing the capacity of its electrolysis plant by another 250,000 tonnes per year, but this project has not yet been implemented.
Indonesia Aims to Transform Its Copper Industry
The Indonesian government is moving to radically transform the country's national copper industry by preparing a package of financial measures, including tax incentives for companies that establish production of semi-finished copper products. The goal is to produce items like copper foil and rolled products for use both domestically and for export to the global market. Currently, the main product of Indonesia's copper industry is pure metal, which is mostly exported. The government now seeks to change this situation to align with global industrial trends.
Copper foil is a necessary component for the manufacture of conductive tracks for printed circuit boards, a key element of all electronic devices, as well as for the anodes of lithium-ion batteries for electric vehicles. Flat-rolled products and pipes are needed for heating, water supply, ventilation, and air conditioning systems, heat exchangers, and electrical equipment. By stimulating the mass production of these goods, Indonesian authorities aim to facilitate their supply to car factories and electronics manufacturers located within the country, while also selling them to countries with significant consumption volumes.
The Indonesian government has been restructuring its non-ferrous metallurgy industry for some time, and the copper sector is no exception. In 2020, it banned the export of nickel ore and concentrates, which led to an increase in the production and shipment of pure nickel, nickel pig iron, and ferronickel. A similar ban on copper raw materials was planned for 2023 but was postponed to 2024 to accommodate the launch of two large new metallurgical plants built by the American company Freeport-McMoRan and the Indonesian company Amman Mineral Nusa Tenggara. In particular, Freeport-McMoRan has commissioned a plant with a capacity of 650,000 tonnes of copper cathodes per year, at a cost of $3.7 billion.
The Indonesian government expects that the transformation of the country's copper industry will increase state budget revenues through the export of high-value-added products and strengthen its position in the global copper market, especially amid the expected growth in demand driven by the development of green energy.