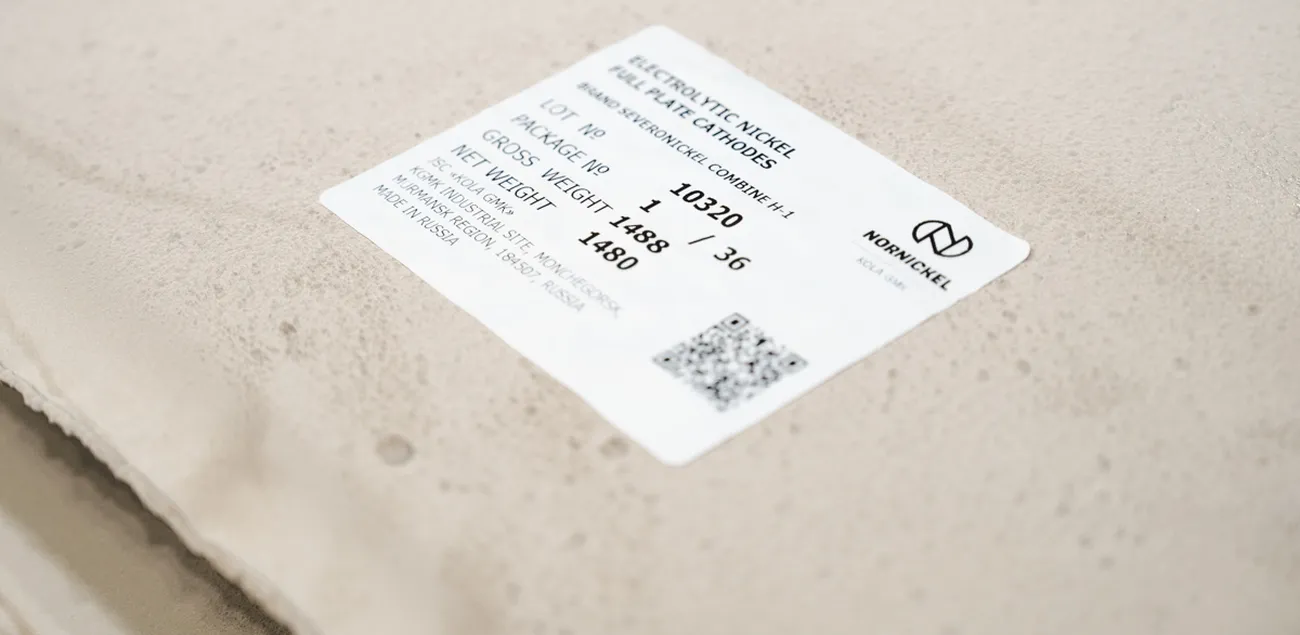
Nornickel, Russia’s largest metals company and the world’s leading producer of refined nickel and palladium, has deployed QR code tracking technology at its Kola Mining and Metallurgical Company facility in Russia’s Murmansk region, enabling customers to access basic product information through mobile scanning. The system provides batch identification, weight data, and manufacturing details for the facility’s 170,000 tonnes of annual nickel production, representing the company’s initial step toward comprehensive digital product documentation across its operations.
Technology Adoption Follows Industry Trends
The metals industry has increasingly adopted digital tracking systems as companies seek to address supply chain transparency requirements and operational efficiency improvements. Major mining companies including Rio Tinto, BHP, and Vale have implemented various digital documentation systems, while metal exchanges have supported electronic trade settlement processes to reduce paperwork and improve transaction speed.
QR code implementation in industrial applications has grown substantially across manufacturing sectors, with companies reporting inventory management improvements and reduced manual data entry errors. The technology offers particular advantages for high-volume commodity trading where rapid product verification and automated data capture provide operational benefits to both suppliers and customers.
Limited Initial Scope Reflects Cautious Approach
The Kola facility’s QR code system currently provides basic product information including batch numbers, weight specifications, and manufacturing location data. Nornickel has indicated plans to expand the system’s capabilities to include quality certificates, chemical composition details, and environmental impact data, though implementation timelines remain unspecified.
The company’s approach contrasts with more comprehensive digital tracking systems deployed by some competitors, which incorporate real-time production monitoring and integrated supply chain management capabilities. Industry analysts note that Russian companies have generally adopted more conservative approaches to digital transformation compared to Western counterparts, often prioritizing operational stability over technological innovation.
Market Context Shapes Implementation Strategy
Nornickel’s digital marking initiative occurs within a challenging market environment for Russian metal producers, who face ongoing international sanctions and restricted access to Western technology suppliers. The company’s focus on customer service improvements through digital tools may reflect efforts to maintain competitiveness in global markets where supply chain transparency has become increasingly important.
European and North American customers have demonstrated growing preferences for suppliers who can provide comprehensive product documentation and traceability information, particularly in automotive and electronics applications where regulatory compliance requirements continue expanding. However, geopolitical tensions have complicated Russian companies’ ability to serve these markets regardless of technological capabilities.
Production Scale Provides Implementation Foundation
The Kola facility processes sulfide ores from local deposits and concentrates from Nornickel’s Arctic operations, producing refined nickel cathodes primarily for European customers. The facility’s established customer relationships and standardized production processes provide a suitable testing ground for digital tracking technology before potential expansion to other Nornickel operations.
Nornickel’s total nickel production of 205,100 tonnes in 2024 positions the company among global industry leaders, though the company faces operational challenges including aging infrastructure, environmental compliance requirements, and restricted access to Western equipment and technology due to international sanctions.
Future Expansion Plans Remain Uncertain
Company officials have outlined intentions to extend QR code implementation to copper, cobalt, platinum, and palladium products, though specific timelines and investment requirements have not been disclosed. The expansion would require substantial additional infrastructure development and process modifications across multiple production facilities.
Industry observers note that comprehensive digital tracking system implementation typically requires multi-year development periods and significant capital investment, particularly for companies operating older industrial facilities that require extensive modernization. Nornickel’s ability to execute planned expansions may depend on continued access to compatible technology suppliers and adequate financial resources.
Operational Challenges Affect Implementation Scope
The digital marking system requires extensive process automation and equipment upgrades throughout the production chain, representing substantial capital investment for a company facing financial pressures from sanctions and reduced market access. Nornickel has not disclosed specific investment amounts or return expectations for the digital tracking initiative.
Russian companies have faced increasing difficulties accessing Western technology suppliers and software platforms, potentially limiting the sophistication and interoperability of digital systems compared to international standards. These constraints may affect the system’s ability to integrate with customer operations or meet evolving industry requirements for supply chain documentation.
Company Background and Market Context
Nornickel operates integrated mining and smelting operations primarily in the Norilsk region of Siberia and the Kola Peninsula, producing approximately 17% of world nickel output alongside substantial platinum group metals production. The Kola Mining and Metallurgical Company represents one of Russia’s oldest metallurgical enterprises, operating since 1935 with established customer relationships across European markets.
The facility serves stainless steel manufacturers, battery producers, and chemical companies requiring high-grade nickel products for specialized applications. However, international sanctions have complicated the company’s ability to maintain traditional customer relationships and access Western markets, creating pressure to enhance competitiveness through improved customer service and operational efficiency.
Nickel serves as an essential component in stainless steel production, electric vehicle batteries, and aerospace applications, with global demand reaching 3.3 million tonnes annually. The metal’s strategic importance has increased with electric vehicle adoption, while supply chain security concerns have driven customer interest in product traceability and supplier verification systems across the industry.