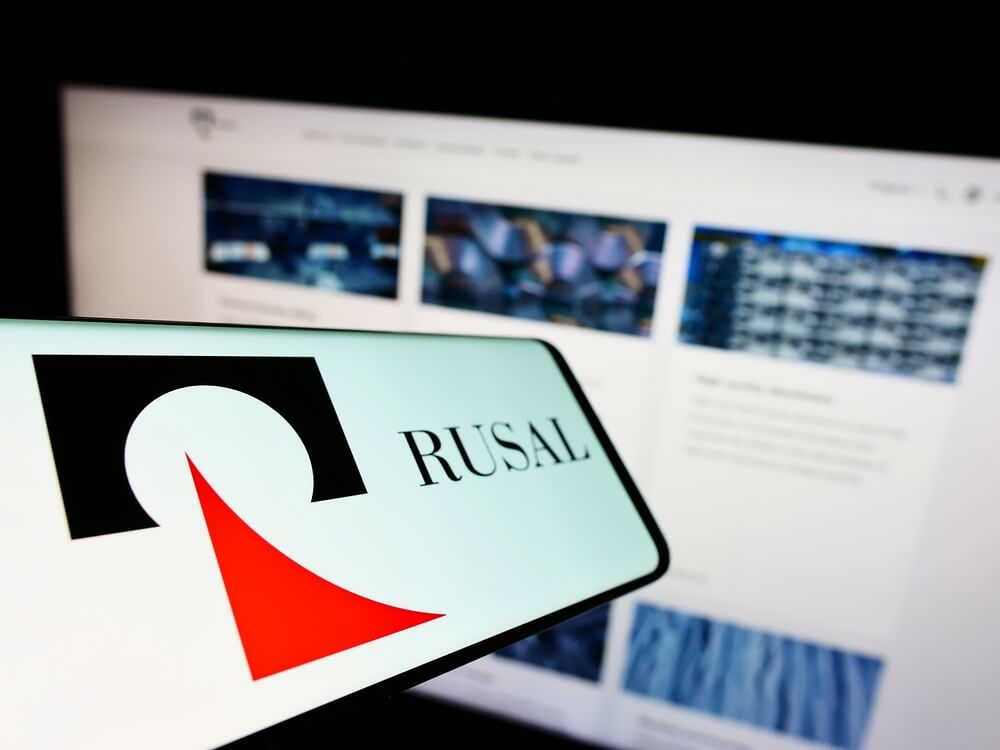
Rusal has achieved a breakthrough in primary aluminium production by significantly reducing vanadium and other heavy metal content using revolutionary inert anode technology. This advancement enhances the electrical conductivity of aluminium, opening new opportunities for its application in the power industry.
The inert anode technology, a key development in aluminium smelting, allows for the production of aluminium virtually free from impurities like vanadium, which traditionally entered the metal through carbon anodes. “The reduction of vanadium content to microscopic levels, practically to zero, is a defining feature of aluminium produced using inert anode technology,” said Victor Mann, Rusal’s Technical Director. “This remarkable characteristic will allow our customers to reliably distinguish our metal.”
Vanadium and other heavy metals have historically been present in trace amounts in aluminium due to the use of carbon anodes, which are made from petroleum coke. These impurities, though minimal, reduce aluminium’s electrical conductivity. Aluminium rods are extensively used in the power industry for cables, ranging from main networks to household wiring. By eliminating such impurities, Rusal’s “inert” aluminium offers energy-saving advantages and minimises power losses, according to Alexander Krokhin, Rusal’s Director of Foundry Technologies and New Products Development Department.
Previously, reducing vanadium content required expensive metal refining processes. The inert anode’s advanced composition, developed after years of research, provides a cost-effective and environmentally friendly solution. “This technology addresses a range of technical and environmental challenges in electrolysis, achieving minimal vanadium and heavy metal content,” said Alexander Gusev, Director of Rusal ITC’s Inert Anode Electrolyser Project.
Rusal pioneered industrial testing of electrolysers with inert anodes in 2017, becoming the first in the world to implement this technology. Unlike carbon anodes, which release greenhouse gases during electrolysis, inert anodes release oxygen, making the process significantly more sustainable.