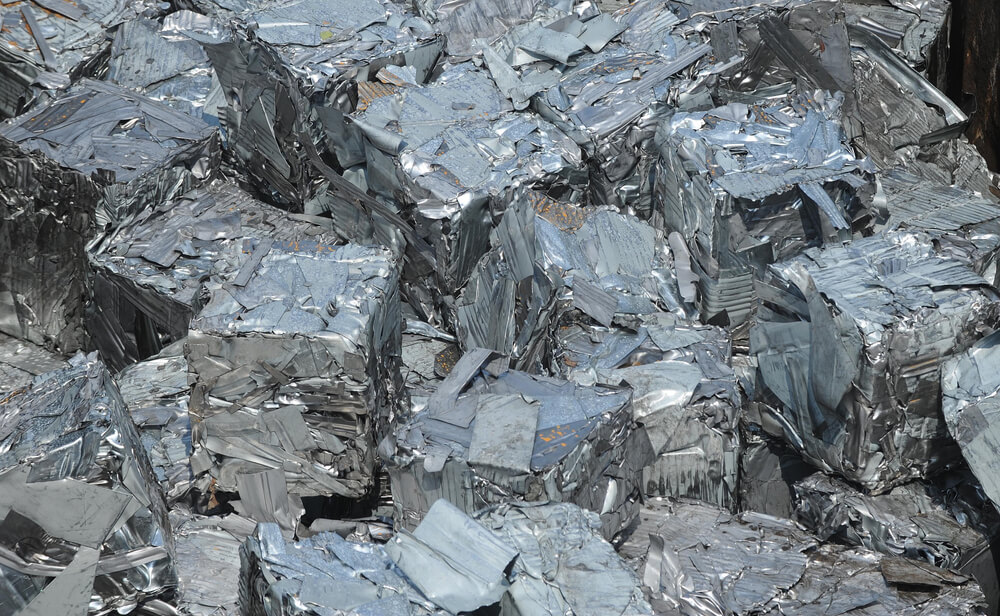
St. Louis-based Phinix has initiated a two-year, $1.8 million cost-shared project funded by the Remade Institute in Rochester, New York. The initiative, titled “Commercial Removal of Fe and Mn from Molten Aluminum Scrap Melts,” aims to enhance the quality and sustainability of recycled aluminum by eliminating metallic impurities from aluminum melts.
This project builds upon a 2024 Remade-funded research initiative and employs patent-pending technology to remove iron and manganese impurities. By improving the quality of recycled aluminum, the technology expands its potential applications, offering an alternative to high-cost, high-carbon primary aluminum derived from bauxite. Phinix, led by founder and CEO Subodh Das, Ph.D., emphasizes the importance of this innovation in reducing reliance on imported primary aluminum while strengthening the domestic aluminum supply chain.
The project brings together a consortium of U.S. secondary aluminum producers, industrial and academic research institutions, industry consultants, and component suppliers to drive commercialization and industry adoption. Collaborators include Worcester Polytechnic Institute, Kingston Process Metallurgy, Smelter Service Corp., Certified Flux Solutions, Audubon Metals, Real Alloys, and Spectro Alloys. Together, these partners represent approximately 50% of U.S. secondary aluminum production capacity, according to the Remade Institute.
Phinix aims to position domestic aluminum scrap as a high-value input for advanced manufacturing applications. The company notes that a significant portion of U.S. aluminum scrap is currently exported, downcycled, or landfilled, which limits its value and increases environmental impact. By increasing the use of recycled aluminum in domestic manufacturing, the project seeks to minimize waste and reduce the aluminum industry’s carbon footprint.
Traditional recyclers address impurities in aluminum scrap by diluting it with purer primary aluminum metal. Phinix’s alternative method directly removes iron and manganese from molten aluminum, a process that has been successfully demonstrated with research partners. The company is now scaling up the process at commercial facilities to facilitate broader industry adoption.
“We are thrilled to collaborate with both existing and new secondary aluminum producers across the U.S.,” Das said. “Our goal is to upgrade abundant, low-carbon domestic aluminum scrap, reducing reliance on costly, high-carbon imported primary aluminum while strengthening the sustainability of the aluminum supply chain.”
Phinix is also seeking additional strategic partnerships to accelerate the adoption of its technology and drive a more sustainable, circular aluminum economy.